Let the water flow!
With 30,000 cubic metres of water per hour, the cooling water requirement of the customer has now been covered.
Kremsmueller secured the cooling water requirement in the factory of a leading steel treatment group. The customer had continuously expanded the capacity of the factory. This increased the requirement for cooling water. When the water from an adjoining stream was not enough any more, a new water concept was developed. A river 2.3 kilometres away had the lead role in this concept. Kremsmueller set up the connection between the river and the factory with 7,400 metres of piping. Two inlet and outlet pipes each ensure optimum operational reliability. Various connecting and branch pipes were laid underground.
Before the welding experts from Kremsmueller could get to work, they had to pass a craftsmanship skills test at the site. Only those who qualified under the strict supervision of an external expert would be permitted to carry out welding work in the project. Thus, first-class weld seams were ensured from the beginning.
The steel pipes, of up to DN 1600, carry up to 30,000 cubic metres of water per hour. The water is pumped into the customer’s factory through "the tunnels and bridges" of the pipeline. When it has done its job, it is led back. Of course, without having caused any environmental pollution. Thanks to the height difference, a turbine can be used for environment-friendly energy generation from the return flow.
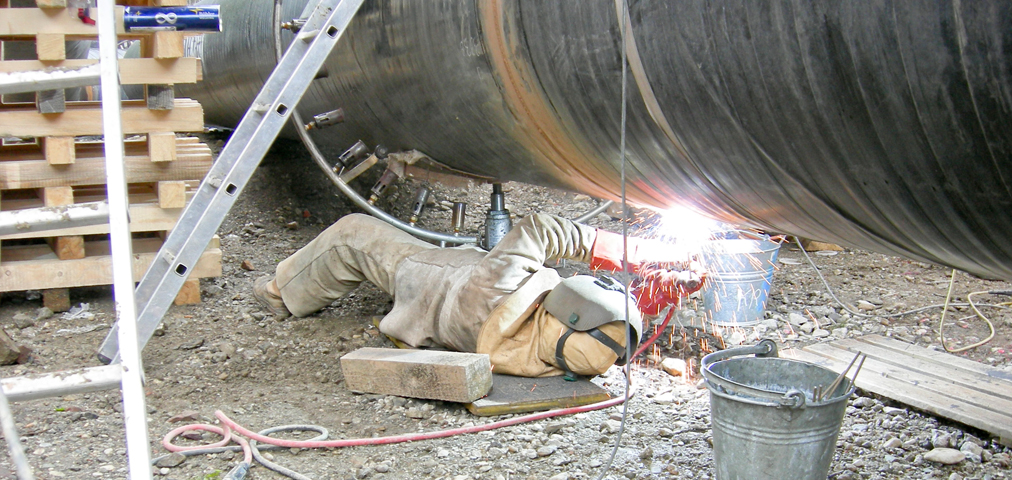
